We took our caps off to you 45 years ago.
With good reasons!
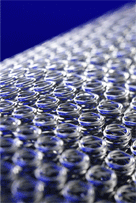
Much publicity has been made about adding caps to the top of coiled springs, claiming that this provides benefits. Contrary to these claims, intensive research and testing done over 45 years ago
proved just the opposite!
Many leading manufacturers of flatwork ironers in the 1960’s and 1970’s provided rolls equipped with individual coil springs including caps on top. SPRINGPRESS was developed and perfected without caps after considering the input of the engineering departments of these manufacturers. The following are the ADVANTAGES to SPRINGPRESS without caps.
No caps to come off.
Anyone who has replaced needlefelt padding knows how hard it is to peel off. SPRINGPRESS has no hooks and still holds the padding so that it never moves. A problem with caps is that the fibers of the padding adhere to them, and the hooks in the caps make it worse. Eventually, replacing the needlefelt will cause some of the caps to come off, resulting in a wet spot forever!
If a severe jam should occur in the ironer, SPRINGPRESS springs may slide along the strip, but this causes no real damage and can be easily repaired with a screwdriver and pliers. If a severe jam occurs in an ironer with springs that cannot move and have caps, many times the wire or strip breaks. In other cases, the caps bend backward and sit at a 90 degree angle, which causes them to perforate through the padding and scratch the chest.
No height re-calibration necessary.
As users of laminated springs know, the adhesion of old padding to the springs is so great that pulling it off causes the height of the springs to increase, making it necessary to re-calibrate the springs before re-padding. The same thing happens when caps are on the top of coil springs. They become elongated and without re-calibration, result in overpadded rolls and loss of padding life and production.
Solid metal stops water droplets.
The solid metal portion of caps prevents water droplets from escaping through the exhaust system without finding a way around the solid barrier. This reduces the drying capacity of the ironer. Eventually the padding becomes clogged and the vacuum system removes less evaporated moisture.
Perforated strips and punched caps are not needed for sufficient exhausting of water vapor.
The space between wires of SPRINGPRESS and underneath the strip is always greater than the sum of the roll perforations, so the vacuum system is properly balanced with SPRINGPRESS. Too much vacuum will cool down the ironer, which is a disadvantage when trying to dry wet material.
The small diameter of SPRINGPRESS divides the pressure much more evenly, resulting in better ironing quality.
Coiled springs with caps have much larger diameter than SPRINGPRESS without caps. Each square meter of ironing surface holds only 2.200 coiled springs with caps, compared to 4.600 SPRINGPRESS springs for the S type or 6.400 SPRINGPRESS springs for the H type. The result is less ironing quality for the springs with caps.
The conclusion is that caps on coiled springs are a step backward, not an improvement.
This is a classic example of trying to be different only to have some sales arguments.
This is definitely not in the best interest of the end user!